Processo PCP na WEB
Objetivo
Apresentar o processo do PCP Centrium, com gerenciamento de OP pela Web.
Compatibilidade
Versão 13.00 ou superior
Requisitos
- Módulo Vendas
- Módulo PPCP
- Parâmetros Gerais:
- PRM0059 – Operador Padrão para o PCP
- Preencher o código no campo “Inteiro1”
- PRM0124 – Gera OP após inserção do item no pedido de venda
- Preencher campo Char1 com S ou N.
- Obs: para as empresas que trabalharem com Plano de Produto, manter esse PRM = N.
- PRM0545 – Baixa da matéria prima de acordo com a quantidade apontada do Produto Acabado
- Char1 = S
- Nesse sentido, será necessário apenas o apontamento do produto acabado e a quantidade de matéria prima baixada será equivalente ao PA apontado.
- PRM0604 – Bloqueio de apontamento quando item não tem saldo.
- Char1 = S ou N
- PRM0608 – Apontamento do Produto Acabado sem empenho de materia prima.
- Char1 = S
- PRM0059 – Operador Padrão para o PCP
How To – Configurações Gerais
Motivos de Rejeição
- PPCP > Cadastros > Operacionais > Motivo de Rejeição
- Cadastrar aqui os motivos que podem causar o refugo da produção.
Setores
- PPCP > Cadastros > Operacionais > Setores
- Cadastrar aqui os setores do departamento produtivo. Cadastrar pelo menos 1 com a descrição GERAL ou PRODUCAO.
Solicitantes
- PPCP > Cadastros > Operacionais > Solicitantes
- Cadastrar aqui todos os colaboradores envolvidos no processo produtivo.
- Para o apontamento por Código de Barra (Win) se faz necessário cadastrar o crachá do solicitante.
- Os departamentos podem ser cadastrados pela lupa de consulta.
Bens/Centros Produtivos
- PPCP > Cadastros > Operacionais > Bens/Centros Produtivos
- Cadastrar aqui as máquinas ou todo e qualquer bem de automação do processo produtivo.
Grupos de Centro Produtivo
- PPCP > Cadastros > Operacionais > Grupos de Centro Produtivo
- Cadastrar aqui o grupo de máquinas ou equipe de produção.
Operações
- PPCP > Cadastros > Operacionais > Operações
- Cadastrar aqui todas as possíveis operações a qual é necessário passar até chegar no produto acabado.
- Indicar operações terceirizadas ou internas.
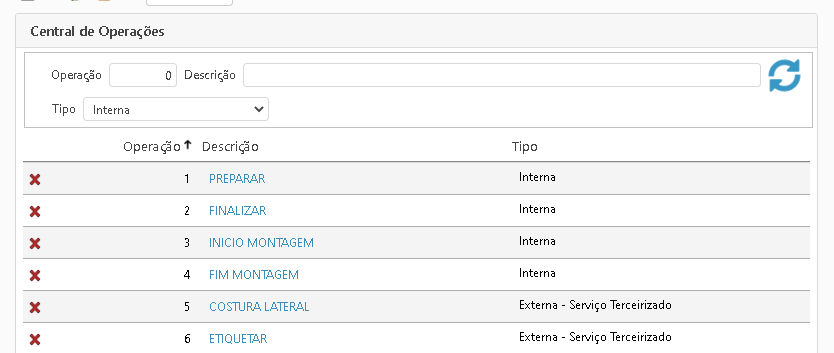
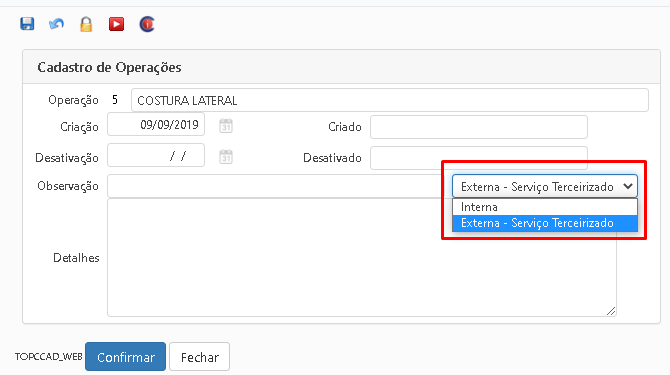
Roteiros de Produção
- Acessar PPCP > Engenharia > Roteiros
- Cadastrar aqui os roteiros de produção, bem como seus processos.
- Os processos podem ter sequencia com intervalo de 10 numero (Ex: processo 10, processo 20, etc.) para, caso houver necessidade de incluir novos processos entre os já cadastrados, a sequencia se mantêm.
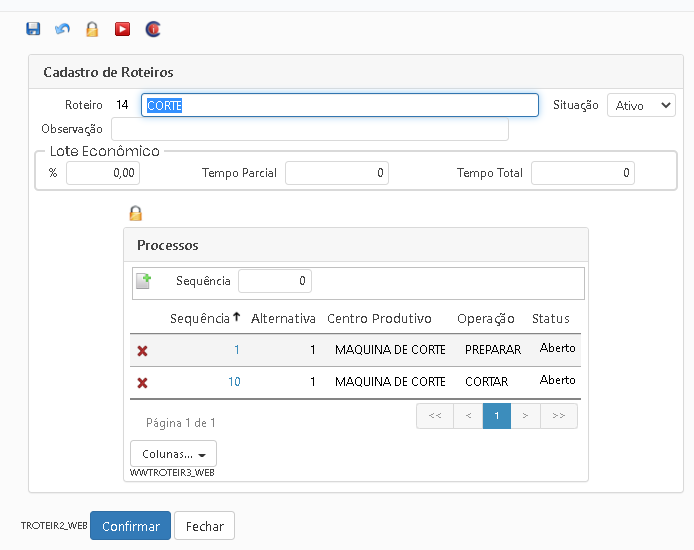
Obs: O roteiro de produção deve ter, no mínimo, 2 processos, sendo o último marcado como ULTIMO PROCESSO.
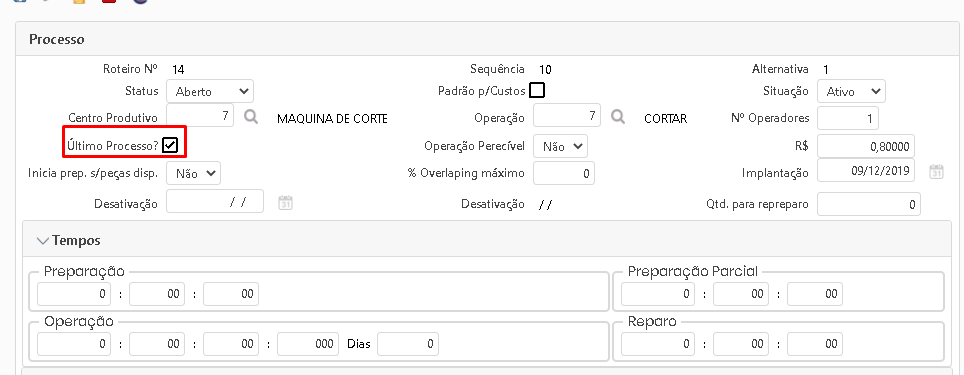
- Na informação do processo, o usuário poderá informar:
- O sequencial do processo e a alternativa (sempre 1, salvo quando houver uma 2ª opção de process);
- Centro produtivo;
- Operação vinculada ao processo;
- Nº de operador para o processo;
- Marcar se for o último processo;
- Em R$, informar o custo do processo (MOD, CIF);
- Informar se o processo pode iniciar sem peças disponíveis em estoque.
- Nos tempos, informar os tempos de preparação, operação, reparo e, ainda, se é necessário uma preparação parcial no processo.
- No detalhamento, o usuário poderá incluir observações do processo produtivo, bem como apresentação da ficha técnica.
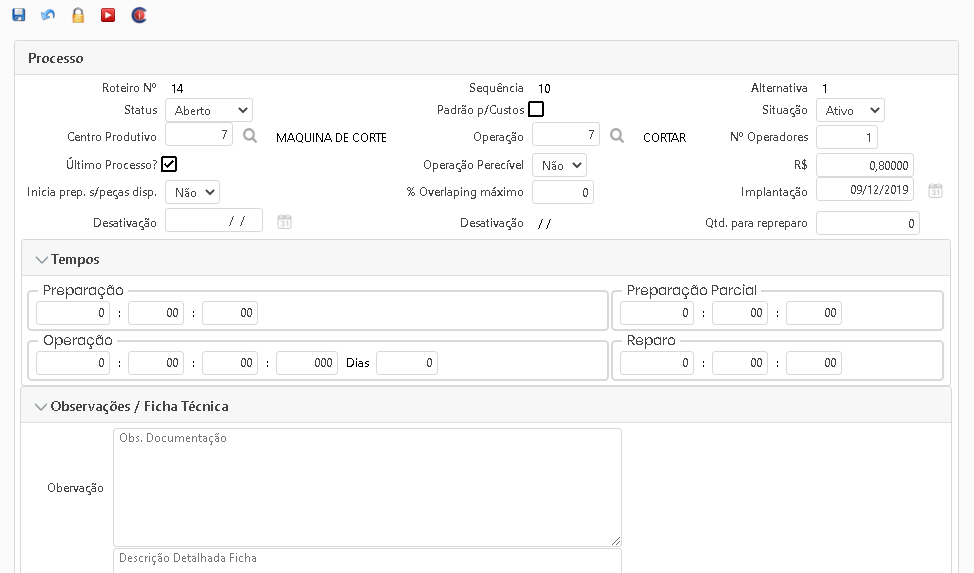
- Ainda no roteiro, caso seja necessário, informar as ferramentas utilizadas para orientar os operadores.
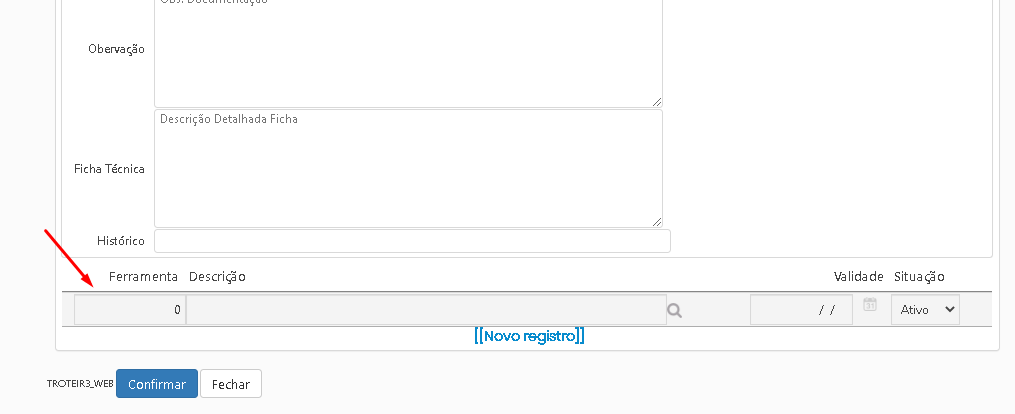
Cadastro de Produto
- Todas as etapas do processo produtivo devem ser finalizadas com algum produto.
- Exemplo: o processo de fabricação de uma camiseta envolve tingir a malha, cortar a malha, costurar, dobrar e embalar. Nesse sentido teremos os seguintes produtos cadastrados no sistema:
- Malha bruta, como matéria prima.
- Tinta para tingir a malha, como insumo.
- Malha tingida, como produto em processo.
- Molde de camisa cortada, como produto em processo.
- Camisa Costurada, como produto em processo.
- Camisa Finalizada, como produto acabado.
Estrutura do Produto
Acessar documentação no link https://wiki.centrium.com.br/pcp/estrutura-de-produtos/
Engenharia do Produto
- Acessar PPCP > Engenharia > Engenharia de Produto.
- A engenharia do produto é o link feito entre O QUE EU PRECISO PARA PRODUZIR (Estrutura do Produto) e QUAL O PROCESSO UTILIZADO PARA PRODUZIR ESSE PRODUTO (roteiros de produção)
- Todo o produto que possuir estrutura cadastrada já aparecerá na grid de Engenharia de Produto.
- Aqui, o usuário irá incluir o roteiro de produção em cada produto que possui uma estrutura.

Obs: informar a família de produtos
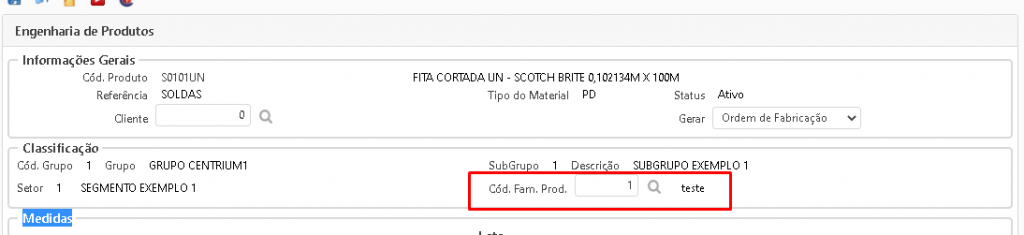
How To – Processos / Operacional
Produção por Demanda – Plano de Produção a partir do Pedido de Venda
A produção por demanda acontece quando a empresa não mantêm um estoque do produto, apenas há a produção com base no pedido do cliente (venda).
Nesse processo, o plano de produção é gerado a partir do pedido de venda.
- Criar o pedido de venda.
- Na Central de Pedido de Venda, opção AÇÕES > GERAR PLANO DE PRODUÇÃO.
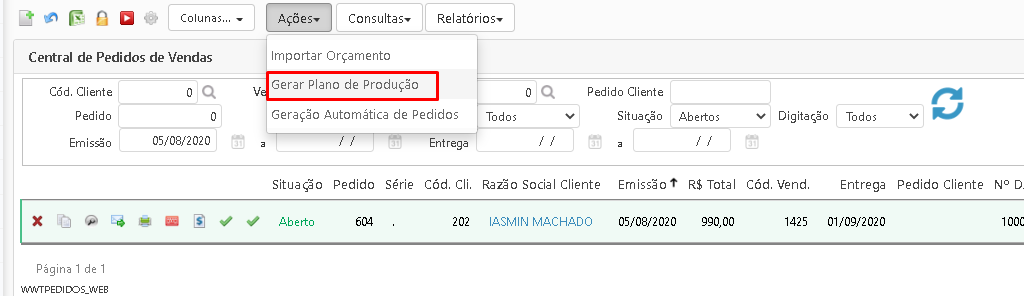
- Validar: a validação vai verificar se o produto acabado possui estrutura cadastrada.
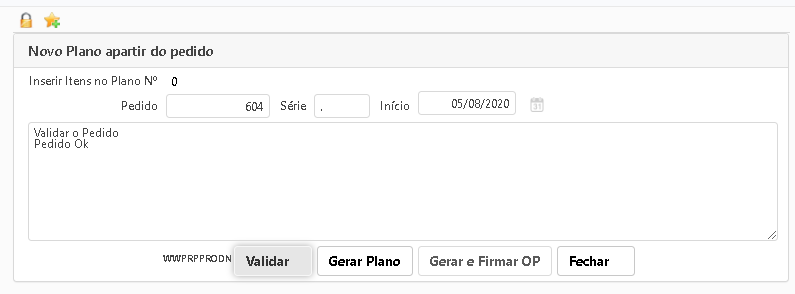
- Gerar e firmar OP: caso a empresa não utilize o plano de produção, poderá gerar e firmar as OPs diretamente para a produção.
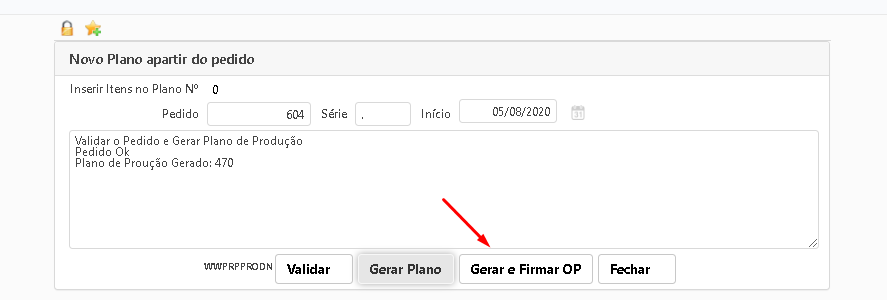
- Gera Plano: para gerar o plano de produção a partir do pedido de venda.
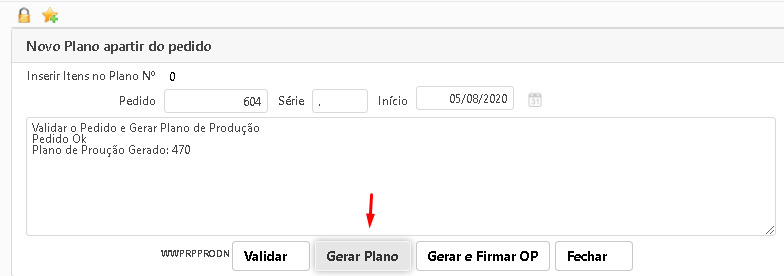
Assim, o Plano de Produção é gerado com o código do cliente vinculado, indicando a produção por demanda.
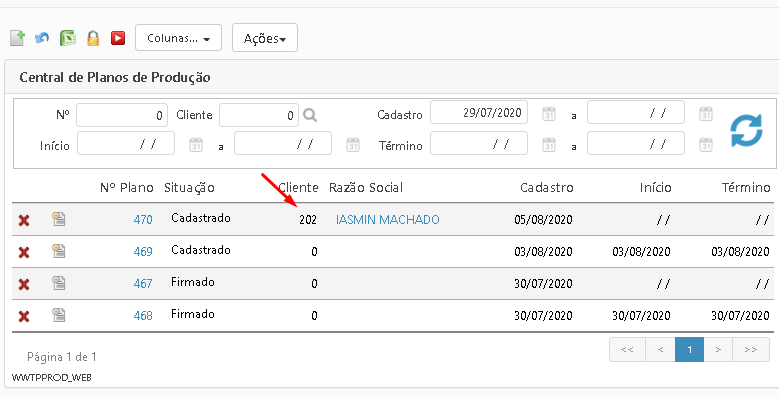
Plano de Produção
- Acessar PPCP > Programação > Plano de Produção.
- Na Central de Plano de Produção é possível encontrar os Planos de Produção gerados pelo pedido de venda ou criar um Plano de Produção Manualmente.
- Os Planos de Produção fazem parte do planejamento da produção e pode ser criado como programação semanal, quinzenal ou mensal da produção, levando em consideração a capacidade produtiva.
Gerando o Plano de Produção manualmente
- Incluir um novo registro.
- Na capa do Plano de Produção, atentar-se ao campos de data de início e término da programação e Centro de Custo. Os demais campos são preenchidos automaticamente.
- O campo “CLIENTE” é preenchido apenas quando a produção for por demanda (vem automático do pedido de venda).
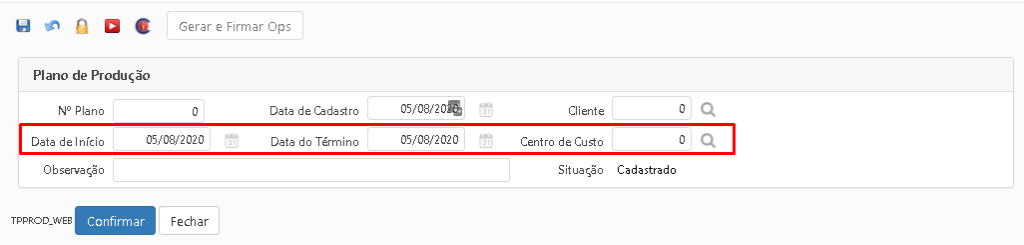
- Após confirmar a capa, o sistema irá permitir a inclusão dos produtos com produção programada.
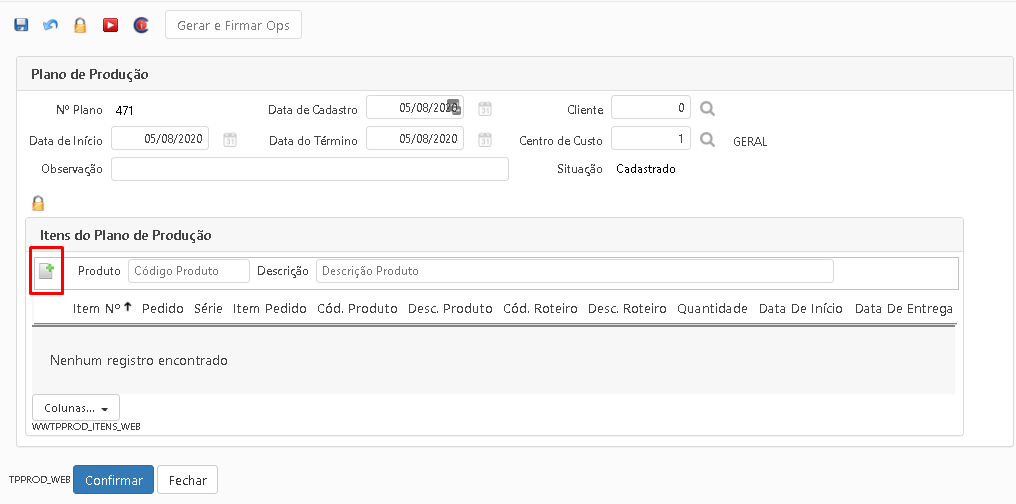
- No produto do Plano de Produção, informar o produto a ser produzido e a quantidade que se pretende produzir.
- Os planos de produção gerados por pedido de venda, já estarão prontos com os produtos acabados e a quantidade a ser produzida conforme venda.
- Note que o roteiro de produção já virá automaticamente informado, buscado da Engenharia do Produto.
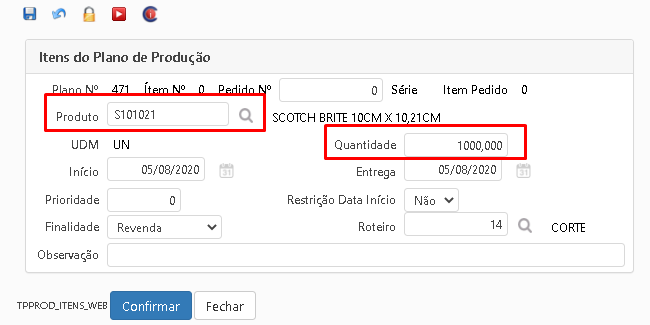
Gerar e Firmar OPs
- Após o cadastro do Plano de Produção, para iniciar o processo produtivo, é necessário gerar e firmar as Ordens de Produção com base no plano.
- Para tanto, no Plano de Produção cadastrado, o usuário deve clicar no ícone para gerar e firmar as OPs.
- Lembrando que GERAR vai criar as OPs e FIRMAR indica que elas estão prontas para iniciar a produção.
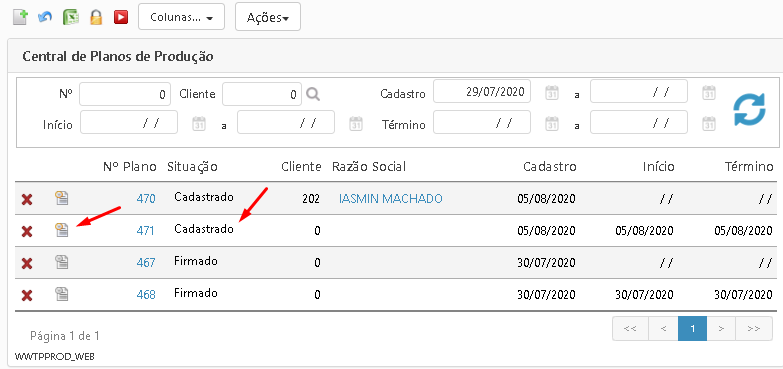
- Marcar as flags para gerar, firmar e gerar empenho de matéria prima, e confirmar.
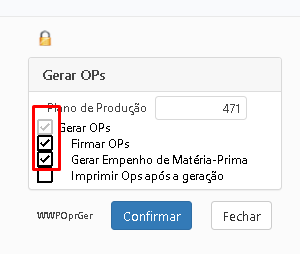
- Ainda, a flag “Imprimir OPs após a geração” poderá ser marcada para gerar a OP em PDF, a fim de repassar para os operadores da produção.
- A OP impressa irá conter a informação do produto final da produção e de sua engenharia (composição da estrutura e roteiro de produção).
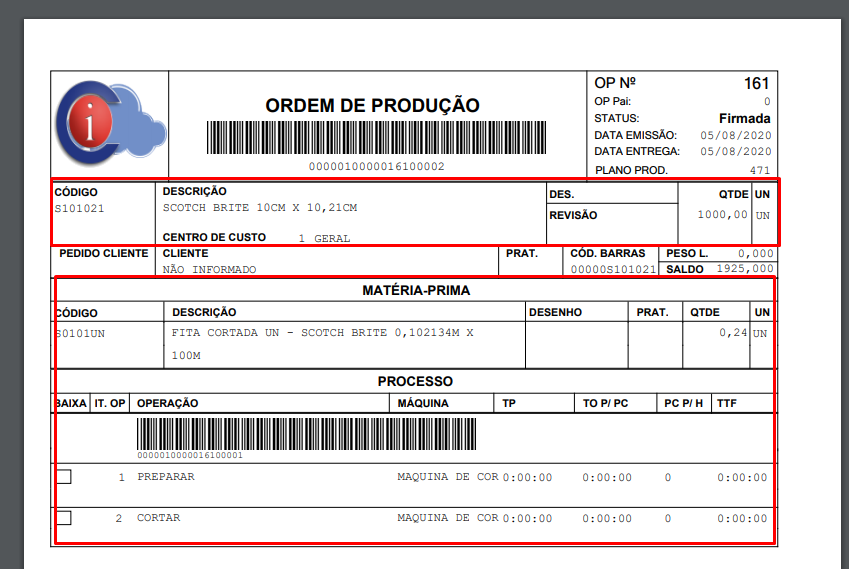
Gerenciamento de OP
- Acessar PCP > Produção > Ordens de Produção.
- Na Central de Ordens de Produção é possível encontrar todas as OPs geradas e/ou firmadas, incluindo as canceladas ou concluídas.
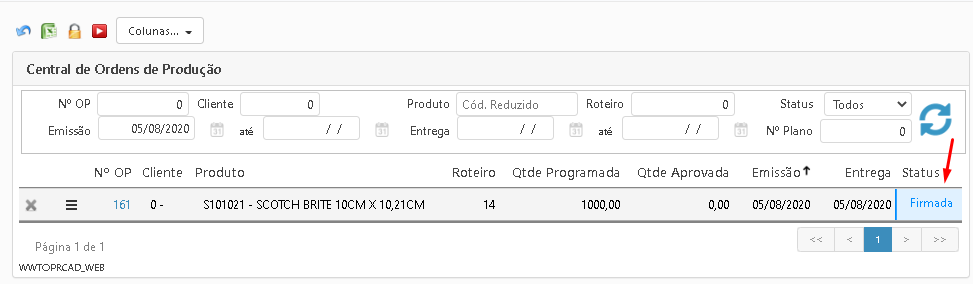
Imprimindo a OP
- Para imprimir a OP, basta que o usuário clique no ícone de AÇÕES > Imprimir:
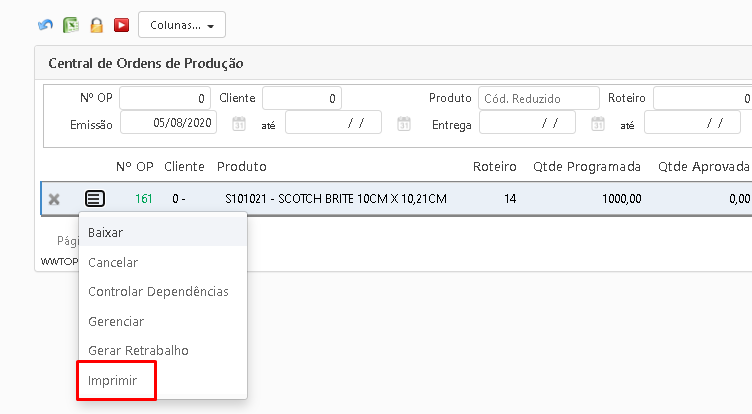
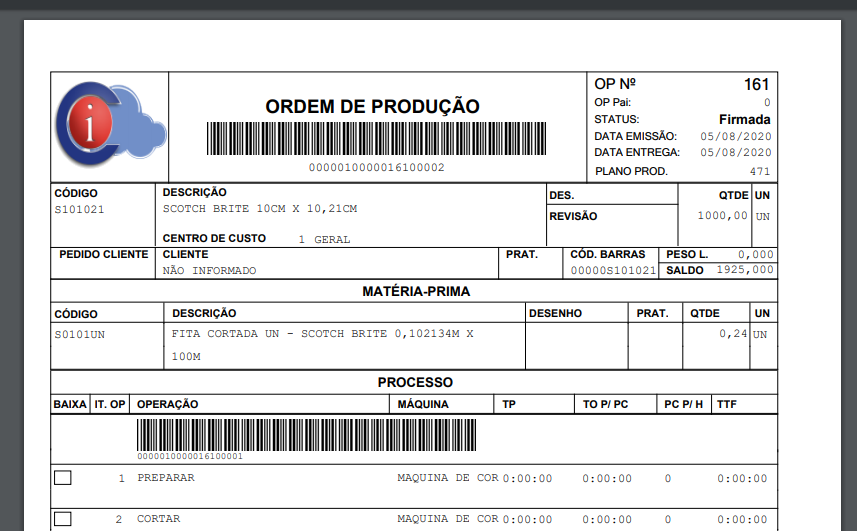
Apontamento da OP
- No apontamento da OP, o operador irá indicar o total produzido e, a partir deste, o sistema irá movimentar o estoque, consumindo a materia prima e inserindo o produto acabado no estoque.
- Para efetuar o apontamento da OP, clicar no ícone de ações > opção GERENCIAR.
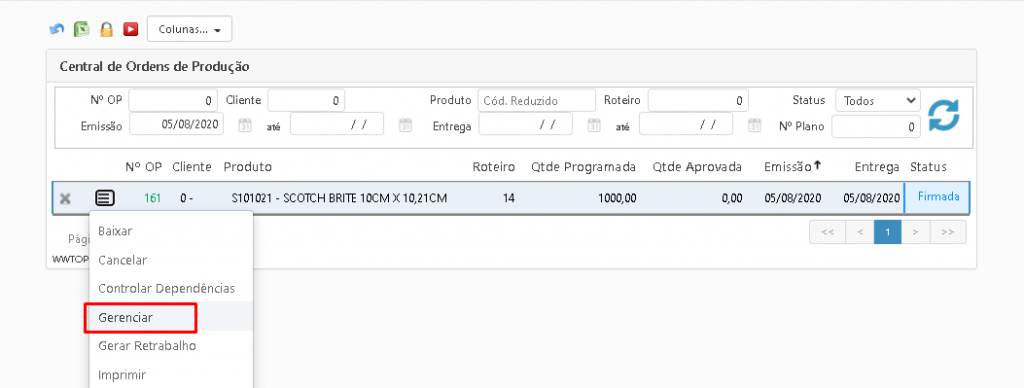
- No gerenciamento de OP, o operador poderá:
- 1 – Incluir outros produtos utilizados no processo produtivo que não fazem parte da estrutura padrão do produto. Exemplo: normalmente o produto vai sem embalagem, mas nesse processo, fora colocado em uma caixa, logo, o operador poderá incluir a caixa como embalagem nessa OP específico.
- 2 – O operado poderá imprimir a OP novamente.
- 3 – Nesse momento, o operador irá dizer ao sistema qual foi a quantidade real produzido, mesmo que for diferente á programada. Com esse apontamento, as matérias primas relacionadas abaixo serão baixadas automaticamente.
- 4 – Concluir a OP, após a finalização do produto produtivo.
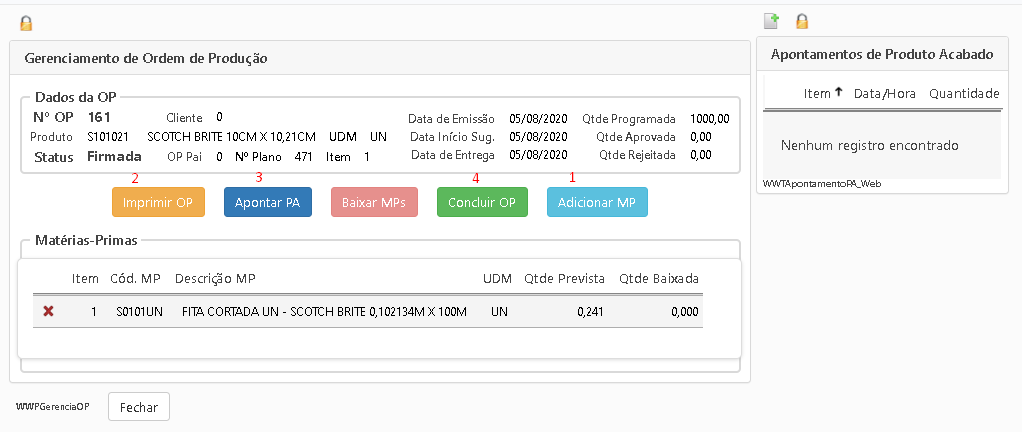
1 – Adicionar MP
Informa a materia prima / componente e indicar a quantidade total que fora utilizada no processo produtivo.
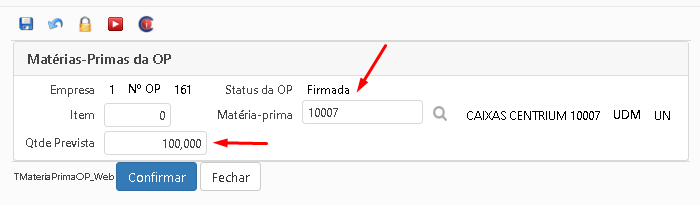

3 – Apontar PA
Para apontar o produto acabado, o operador irá indicar a quantidade produzida, mesmo que não seja igual a quantidade programada. Exemplo:
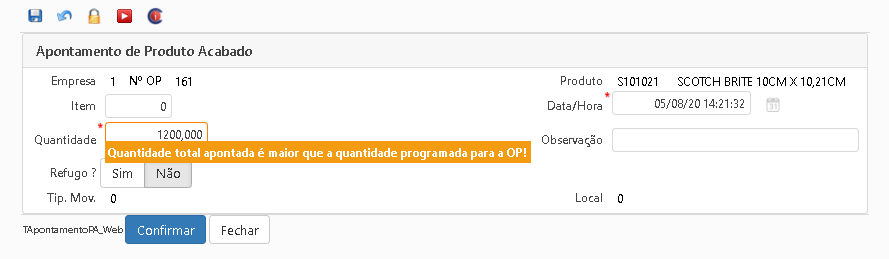
Apontamento do refugo (prdução rejeitada)
- O refugo é a produção com defeito. Nesses caso foi produzido o produto acabado mas, por algum motivo, as peças se perderam. Ou seja, preciso apontar o refugo para consumir a materia prima que fora perdida.
- Nesse sentido, o apontamento do refugo também acontece pela opção 3 – Apontar PA.
- A diferença nesse processo é que a a quantidade informada será a perdida, e a opção REFUGO será marcado = SIM.
- Além disso, é necessário informar o motivo da perda das peças.
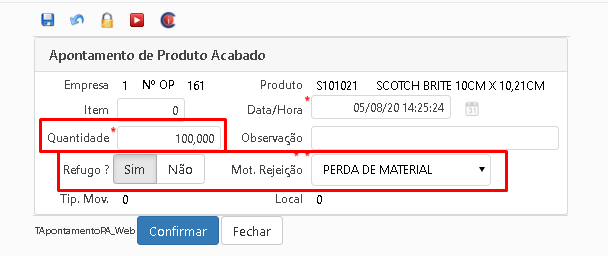
Observação: para a produção rejeitada, será necessário criar uma nova OP manualmente.
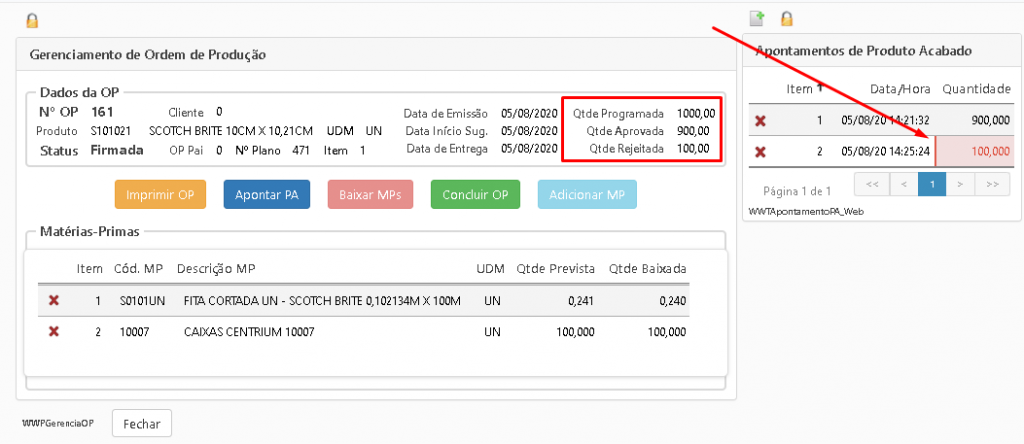
Relatórios do PCP
Necessidade de materiais por Plano de Produção
- Acessar PPCP > Programação > Necessidade por Plano de Produção.
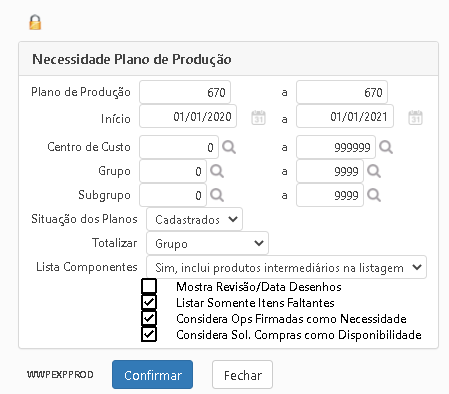
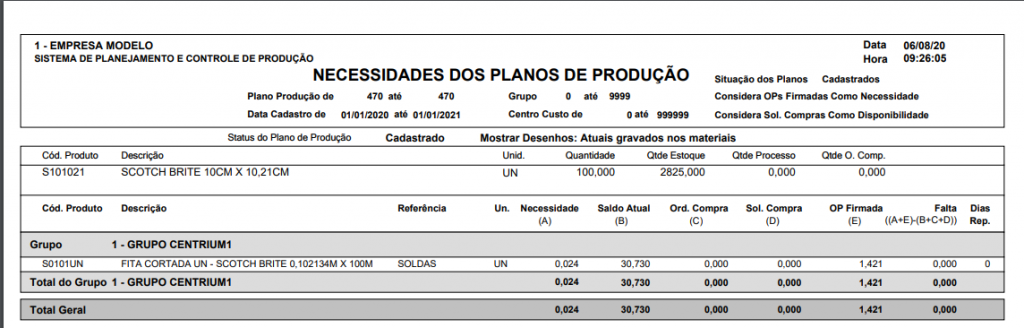
- O relatório irá apresentar na parte superior todos os produtos acabados/em processo das estruturas, sendo estes os produtos principais.
- Na parte inferior, irá apresentar todos os componentes dos produtos principais.
- Na seção de produtos principais, podemos ver que o sistema traz a informação do produto (código, descrição e unidade de medida), além de trazer as informações de quantidade, sendo:
- Quantidade = quantidade programada para produção no Plano de Produção.
- Qtde. Estoque = saldo físico do estoque do produto.
- Qtde. Processo = caso o produto seja encontrado em uma OP em processo, ele apresentará esse estoque. Isso acontece para os produtos intermediários ou em processo, pois os mesmos aparecem como produtos principais (pois tem estrutura própria) e na relação de componentes.
- Qtde. O. Compra = quantidade deste produto que está em Ordens de Compra em aberto, ou seja, com previsão para entrada futura.
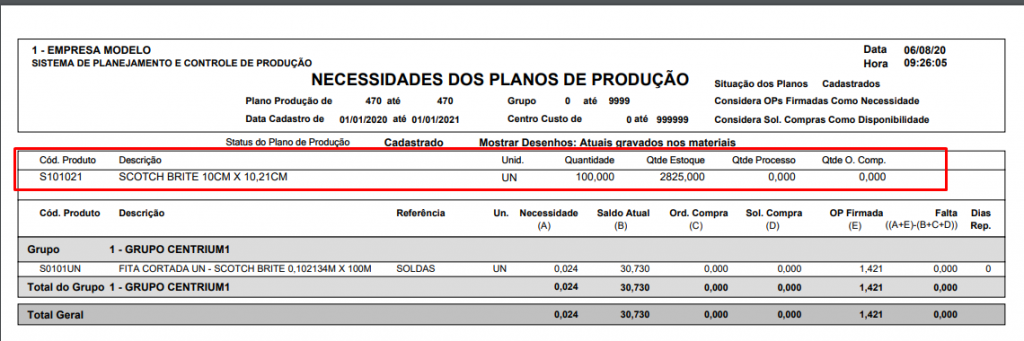
- Na parte inferior, onde mostra o detalhamento dos componentes, o sistema traz algumas informações para análise da necessidade:
- Necessidade (A) = quantidade necessária do componente para essa produção. Dados pela fórmula [Quantidade_do_Plano] * [Fator_Consumo_Estrutura].
- Saldo Atual (B) = saldo físico do estoque.
- Ord. Compra (C) = quantidade do produto em ordens de compra em aberto (não atendidas).
- Sol. Compra (D) = quantidade do produto em solicitações de compra em aberto (que ainda não se transformaram em ordem de compra).
- OP Firmada (E) = Quando o componente já estiver cadastrado em alguma OP que já esteja firmada, o sistema considerará essa quantidade.
- Falta (fórmula) = ([A + E]-[B + C + D])
- [A + E] = estamos fazendo a análise de planos de produção cadastrados apenas (que não tiveram OP geradas) e as OPs Firmadas são OPs que não estão concluídas, ou seja, não houve processo produtivo, logo, para a programação devemos considerar a necessidade do plano de produção cadastrado e das OPs firmadas, pois ambos os casos terão necessidade desse componente no processo produtivo.
- [B + C + D] = essa fórmula representa o que já existe no estoque e o que vai entrar no curto prazo, levando em consideração que se houver ordem de compra ou solicitação de compra, o setor de Compras já está ciente da falta do material para pedido.
- Dias Rep. = dias de reposição. Os prazos médios podem ser trabalhados no sistema, sendo:
- Prazo médio de pagamento a fornecedores = informa na estrutura do produto.
- Prazo médio de estocagem = informa na estrutura do produto.
- Prazo médio de entrega dos fornecedores = informa no cadastro do fornecedor.
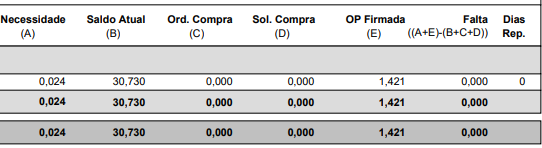